Macalloy engineered and supplied bespoke curved post-tensioning bars, with custom adapter couplers, which run throughout the Diplodocus body structure, from the head to the tail. We offered offsite training on how to install and tension the bars. The Macalloy threaded bar systems not only support the weight of the structure, but the PTFE coated bars provide low visibility and anticorrosion qualities.
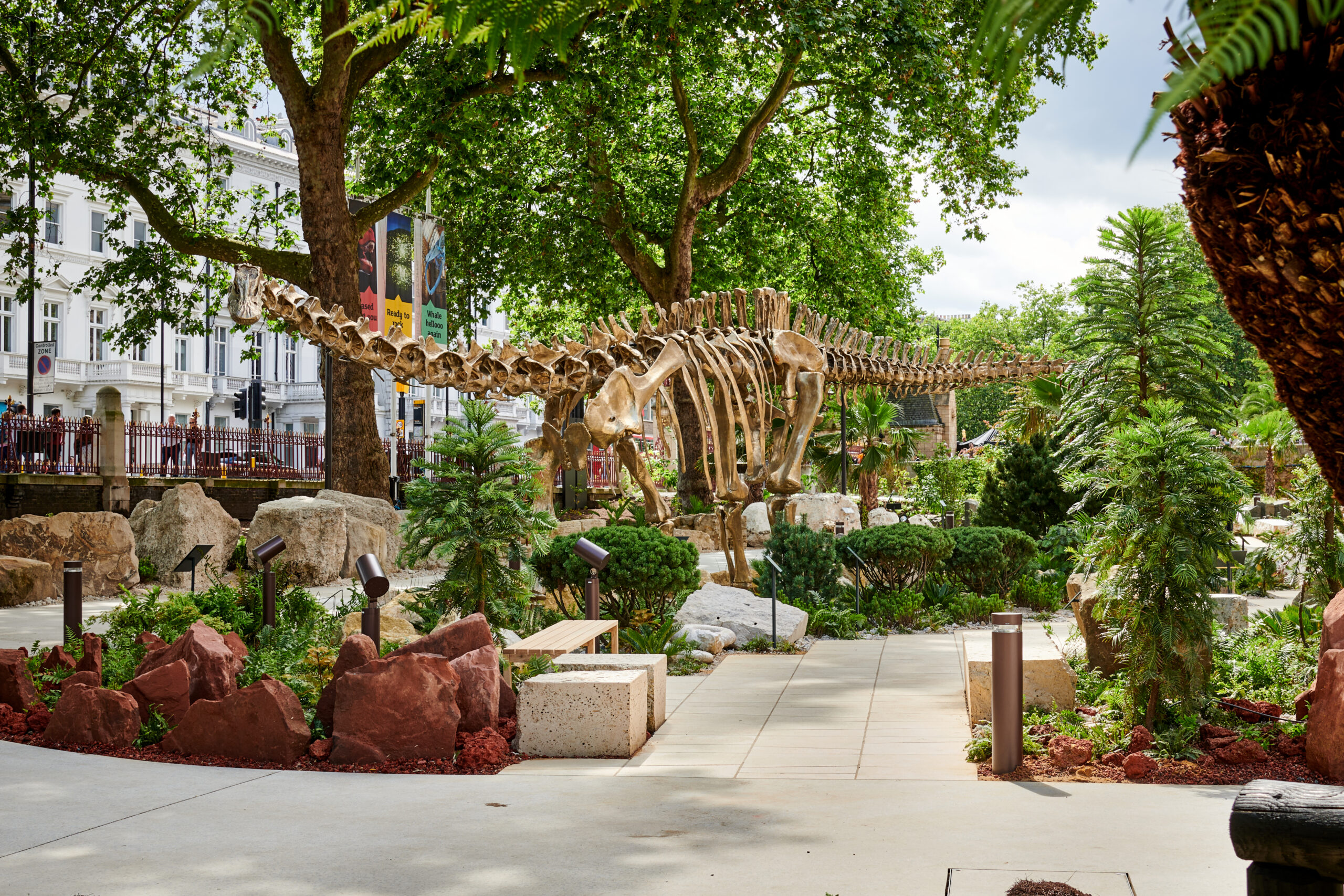
Image © The Natural History Museum, London.
The project required that the Diplodocus (named Fern) would be exhibited permanently in an external environment, exposed to all weather conditions, requiring minimal visibility to the internal structure, and, most significantly, avoid the appearance of being “propped up”.
Macalloy worked closely with Structure Workshop, a London-based engineering firm, to ensure we offered exactly what was needed to complete this one-of-a-kind engineering challenge, as nothing like it had ever been attempted before.
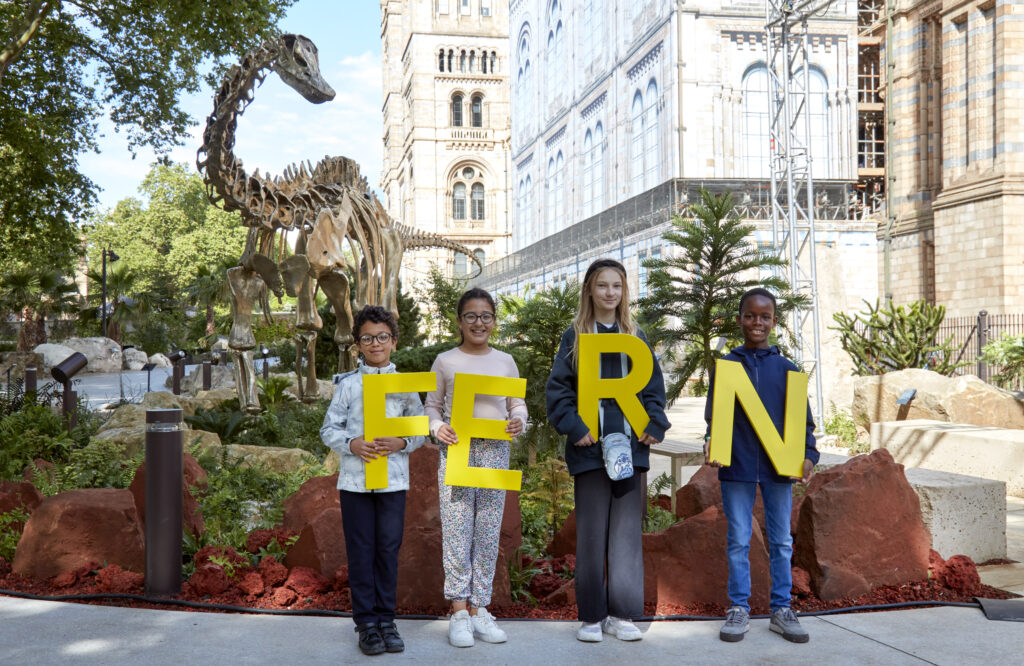
Image © The Natural History Museum, London.
Technical information on the structure
Fern is a life-size bronze replica of the Natural History Museum’s popular Diplodocus cast, also known as Dippy.
Diplodocus was one of the longest animals to have ever lived. Fern, measures 25 metres (the length of three London buses) and made up of 292 bones. The long neck and tail are cantilevers, which means they are only supported from one end.
Bronze is also a heavy material to support, and because Fern will not be protected inside a gallery, the structure may be climbed on, increasing the weight required to be supported.
Due to the specific requirements outlined in the brief, the design team were initially unsure as to whether the project task would be achievable. However, Factum Arte working with London-based engineers Structure Workshop and Madrid-based foundry Fademesa, worked together alongside scientists from the Natural History Museum to design and create the Diplodocus cast.
The entire procedure took about two years, beginning with high resolution 3-D scans and ending with a complete dinosaur cast in bronze.
Macalloy bars support the construction
The Macalloy bars have various features that make them completely unique to the project.
- Precisely engineered, smaller sized bar systems were used to ensure an accurate fit inside the delicate bones at the end of the neck and tail.
- Special adaptor couplers were designed to link smaller bars to larger bars, whilst maintaining its structural capacity.
- They were made with a curvature to match the contour of the dinosaur’s spine.
Compared to typical post-tensioned bars, the Macalloy bars used for this project were significantly smaller. Each component was unique, and the entire production was fully customised.
Tension bars are rather uncomplicated products to use which, provide a significant benefit; the simplicity of the threaded ends allowed the workshop team to easily assemble and disassemble the neck and tail. Throughout the assembly, this had to be done numerous times as the tension forces were set, tested, and modified until the dinosaur was perfectly positioned. As the body and tail were shipped in separate pieces , it was a straightforward task to put them together using the hydraulic Jack and the two Macalloy nuts.
Macalloy engineers provided a one-day training session at our premises on the use of the hydraulic equipment. This included tips and advice on the tensioning process and the safe working use to assist their installation.
The prestressing assembly is the design’s only non-bronze component. The tendons are possibly the most critical part of the entire design since they sustain the heavy weight of the neck and tail under tension. During assembly, a quarter-tonne weight was hung from the neck and tail ends, and the Macalloy bars held the load.
Under load, the Macalloy 1030 system will stretch and relax less than its cable counterparts, which allows for a more robust and rigid structure and minimised movement. The visibility of these manufactured features had to be kept to a minimum so that the dinosaur’s anatomy could be appreciated.
Most crucially, the engineers at Macalloy were able to create a method of fabricating the curved bars that followed the structure of the dinosaur’s spine. Without this innovation, the design would not have been as successful.
Fern the Diplodocus and the Jurassic Garden is supported by Kusuma Trust.
“Macalloy gave us the confidence to go beyond standard designs and created bespoke elements in order to accomplish something amazing and unprecedented. Macalloy provided training and technical assistance throughout fabrication. They showed the Factum Arte team how to install and tension the bars. They were also flexible and refabricated certain elements quickly when necessary.”
Endorsement of Macalloy from Structure Workshop Engineers London

Would you like to discuss a project?
+44 (0)1909 519 200
Give us a call or use the live chat to get a quick answer.